On-site Audits | ACER ESG
Acer’s suppliers must respect labor rights, adopt environmentally responsible manufacturing processes, and provide safe working conditions. We implement the latest version of the RBA Code of Conduct, which encompasses five key areas: labor, health and safety, environment, ethics, and management systems. Acer requires suppliers to conduct regular RBA on-site audits (or obtain SA8000 certification) by third party to ensure compliance with the RBA Code of Conduct and identify deficiencies in the suppliers' execution in the above five areas. Additionally, suppliers are required to implement improvements within a specified timeframe to continuously enhance the social and environmental responsibility of Acer’s supply chain. For suppliers with non-conformance priority finding or challenges in implementing improvement plans, discussions and progress tracking will be conducted via telephone or video conferencing to ensure the timeliness and effectiveness of improvement measures.
In addition to auditing all significant suppliers, we expand our audit scope to fulfill our management responsibilities for supply chain by including subcontractors and key component suppliers in the regular RBA VAP audit by third party,
2023 On-Site Audit Results
More than 210,000 direct supplier employees were audited, 3,394 direct employees were interviewed
Acer uses risk assessment results of the ESG scorecard as the basis for performing on-site audits and assessments.We examine the country risk, manufacturing processes, and products of each supplier, along with results of previous audits, as well as taking into account the concerns of stakeholders when setting out our annual audit plan.
In 2023, a total of 83 audits were conducted, all of which were carried out through on-site audits, including 26 closure audit for non-conformance items and audits for 4 new suppliers. No suppliers were disqualified for failing to meet Acer's social and environmental management requirements. The number of direct employees of audited suppliers in 2023 exceeded 210,000, with 3,394 direct employees interviewed, of which over 80% underwent the RBA VAP. The audit completion rate for audits conducted within a two-year validity period was 92.2%.
Total Implementation Rate of On-site Audits
92.2 %
Percentage of Audits of Higher Risk First-Tier Suppliers
For the three suppliers whose total scores in the 2023 RBA audit were below 120 (out of a possible 200), indicating higher risk, we convened online meetings to discuss improvement plans and review progress. These meetings aimed to provide immediate and effective solutions through feasible discussions and technical advice. Once suppliers demonstrated tangible improvement, third parties completed the RBA closure audits for them. All three suppliers underwent on-site audits, resulting in a total audit coverage rate of 100%.
Audit Methods | % |
---|---|
VAP Audits Performed by a Third Party | 100% |
Total | 100% |
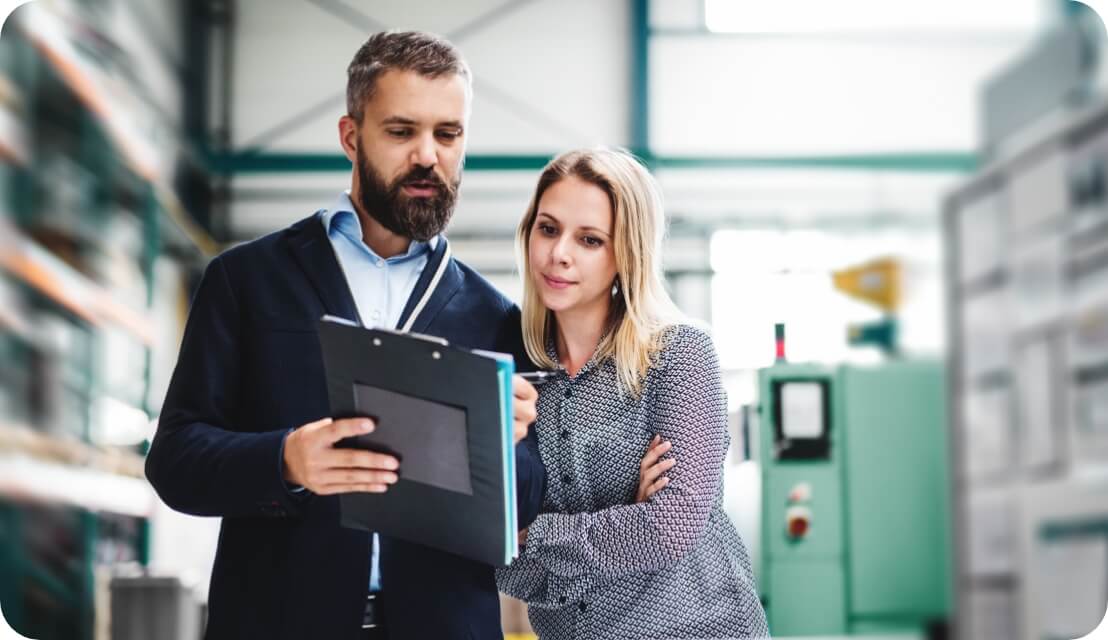
According to the aforementioned details, from 2008 to 2023, Acer has conducted a total of 1069 audits on first-tier suppliers. Furthermore, to effectively enhance the implementation of the supply chain, since 2017, Acer has required first-tier suppliers to conduct risk assessments on their important material suppliers at the next tier before audits. Summarizing the assessments, 6% were classified as high-risk and 23% as moderate-risk. Following this policy, audit activities continued in 2023, with a total of
1145 audits conducted on second-tier factories. Since 2021, Acer has further deepened supply chain execution by extending audit
activities to third-tier suppliers, achieving 693 audits in 2023.
Looking ahead to 2024, we plan to conduct 70 on- site audits of first-tier supplier manufacturing factories, covering 140,000 direct employees and conducting interviews with 2,500 employees. Meanwhile, we have set annual RBA on-site audit compliance targets as follows: labor 87%, health and safety 87%, environment 95%, ethics 95%, and management systems 95%. We will also continue to drive audit activities for second and third-tier suppliers, actively enhancing improvements in labor practices and working environments, and deepening the long-term positive impact on the entire supply chain.
2024 RBA Site Audit Compliance Targets
Labor
87 %
Health and Safety
87 %
Environment
95 %
Ethics
95 %
Management Systems
95 %
Supplier Audit Categories and Number of Audits, 2019-2023
- First-Tier Supplier Audits = VAP (or SA8000) + Full Audit + Surveillance Audit
- Cumulative First-Tier Supplier Audits = Cumulative First-Tier Supplier Audits (Previous Year) + First-Tier Supplier Audits (Current Year)
- Cumulative Total Audits = First-Tier Supplier Audits + Second-Tier Supplier Audits + Cumulative Total Audits (Previous Year)
- The statistical period for each year is October 1 of the preceding year to September 30 of the current year, totaling 12 months.
Manufacturing Supplier Direct Employees and Cumulative Direct Employees Audited, 2019-2023
Manufacturing Supplier Employees and Cumulative Direct Employees Interviewed and Audited,2019-2023
2023 Audit Results Analysis
From on-site audit results, we see that the greatest proportion of non-compliance occurred in labor issues, followed (in order) by health & safety, environmental, management system, and ethics.
Distribution of Non-Compliance Found in Audits
Significant Deficiencies (defined as Priority Non-Conformances) and Other Deficiencies
RBA Code of Conduct Conformance
* Data covers all suppliers subject to audits by Acer management, third parties, and VAP, a total of 98.
Important Issues and Tracking of Improvements in 2023
Labor RightsThe main labor rights deficiencies primarily pertain to working hours and benefits issues. Other deficiencies include the handling | |
Working HoursThe main issue with working hours is primarily due to overtime. The problem of overtime in the manufacturing industry is complex, involving factors such as production efficiency, employee well-being, and compliance with local regulations. To address this issue, it is necessary to analyze labor demand, optimize production processes, provide employee skill training, improve communication and coordination, and identify the causes of overtime. The main strategies for improvement focus on implementing flexible scheduling systems, providing efficiency incentives, investing in equipment and technology, and implementing monitoring and evaluation. In summary, solving this problem requires a sound consideration of the aforementioned factors and the | |
Labor Wages and BenefitsRegarding labor wages and benefits, the main issue often revolves around outdated knowledge and information. Despite significant improvements in 2023 driven by Acer's strong communication and oversight, there are still instances where new employees are unaware of the benefits of social insurance or where employers fail to promptly recognize their updated statutory obligations. Continuous efforts are needed to enhance advocacy and education, explaining to both employers and employees the importance and advantages of social insurance. Providing relevant online training and document sharing can help them | |
Environmental Safety and HealthIn terms of environmental safety and health deficiencies, the main issues revolve around the acceptance of new construction and |
Corrective Action Reports (CAR)
Acer issues Corrective Action Request (CAR) to higher-risk suppliers found to have non-compliance during audits. Upon receiving the report, suppliers are required to submit a written CAR within 30 days. Acer's audit management personnel conduct a written review, and continuous improvement tracking is carried out monthly. Improvement results are confirmed during the following
year's on-site audits. For suppliers with higher audit risk results, Acer adjusts and manages procurement strategies accordingly. In
the 2023, tracking statistics were conducted for the VAP audit scores of suppliers still engaged in ongoing transactions. A total of
135 deficiencies were identified among suppliers with scores below 160 or with priority non-conformance issues. As of December 31, 2023, improvement measures have been implemented for all 135 deficiencies and continuous tracking has been achieved. This includes addressing 5 priority non-conformance issues, all of which have been addressed with a 100% implementation rate
for corrective measures. Additionally, corrective action rates have been provided for other non-compliance issues, with a 100%
implementation rate as well.
Percentage of Priority Non-Conformance with Corrective Measures Implemented
100 %
Other Non-Conformances with Corrective Measures Implemented
100 %
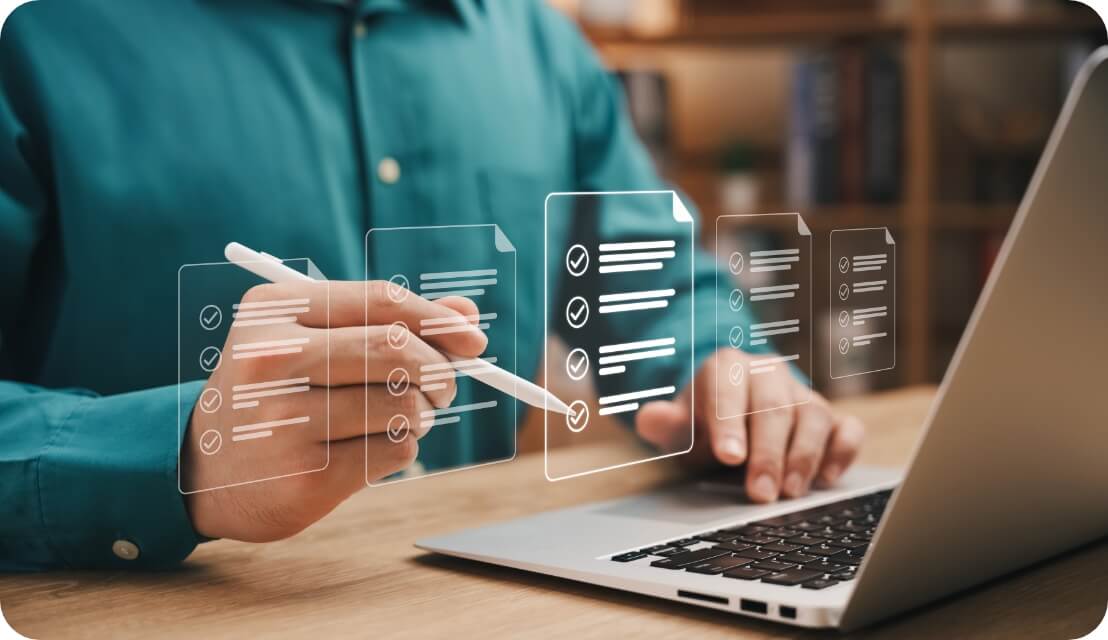
Important Issues and Corrective Actions for On-site Audits